Ever since I became the new caretaker of
Orvil's chisels, I wanted to clean them up and make new handles for them. And having made my
lathe recently, I could finally do it.
 |
Orvil's chisels |
These chisels had gone through some rough use. All the handles were reinforced with steel ferrules at the back end. The ferrules were heavily peened over from who-knows-how-many steel hammer blows. Many of the handles were cracked or broken.
The thing I don't understand is that Orvil Heft was a carver and painter of wooden birds. It's hard for me to imagine that he needed these heavy-use chisels. Perhaps he collected them and didn't use them. Or maybe he had other woodworking interests besides birds. But whatever the case, I wanted to make them nice again to be used every day.
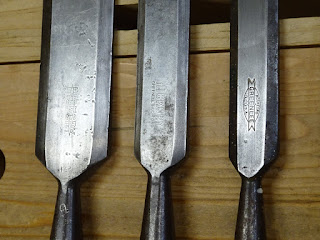 |
The three largest - 1 1/2", 1" and 7/8" - are Greenlee bevel edged chisels |
 |
The five smaller chisels - 3/4", 5/8", 1/2", 3/8" and 1/4" (last two not shown) - are D. R. Barton firmer chisels |
 |
The five largest chisels' handles |
 |
Right three handles are the remainder |
To keep this post from getting too long, I'll go over the rework of the metal parts. Next time I'll write about re-handling the chisels.
Removing the old handles was fairly easy. Some were already loose, but some needed several raps on the benchtop to loosen them. I took sandpaper to the metal - 180 grit and 220 grit.
 |
Four cleaned, four to go |
I was careful to go lightly over the logos. I learned that lesson a couple years ago on a saw that I cleaned up and almost obliterated the etch. Never again ...
When they were clean enough, I flattened the backs. This went faster than I thought it might, thanks in part to the extra-coarse diamond stone that I got last year. But it did take a fair amount of time, especially for the wide chisels. Every one had low spots at the edges, possible due to being flattened on dished stones earlier in life.
 |
Flattening the 7/8" chisel - note the oval scratch pattern,
showing sides and leading edge were low |
Every one of these chisels was severely dull. The 7/8" chisel had a big chip off one corner. The 1/2" chisel had been rounded at the cutting edge. And I'll get into the 1/4" chisel a little later. All needed to be ground back to get past the rounded-over corners of the cutting edge.
 |
Chip out of the 7/8" chisel |
 |
7/8" chisel ground straight across ... |
 |
... but this came at a price - there was a lot of material to remove to grind a new edge |
OK, about that 1/4" chisel. The leading edge had been ground to be 3/16" wide and the grinding started about 3/4" back from the leading edge. I thought for a long time about what to do. I really didn't want to remove 3/4" of usable metal and throw the length out of whack with the rest of the chisels. My other option was to make this chisel into a 3/16" chisel. I didn't have a 3/16" chisel, so that's what I did.
I'm not set up to do metal work. But I went for it anyway. Lacking layout fluid, I used a Sharpie marker to blacken the flat side and the bevel side near one edge.
 |
Using Sharpie to lay out the metal to be removed |
 |
Then used a marking gauge set to about 1/32" to mark a line on the black ink |
 |
Used a round chainsaw file to cut in to the gauge line as far back as I would remove metal.
This was just shy of the D.R. Barton logo, which is on the side of the 1/4" chisel
(the logo is on the bevel side of all other sizes) |
 |
Filed to the line |
On the first side I did, I tried to file straight across. But on the second side, I filed "skyward" from both directions to leave a peak in the middle.
 |
Peak in middle after filing from both directions to the layout line |
 |
Then I marked the edges and filed the middle, trying not to remove the black marker all the way to the edges. |
After the filing, I took the sides to the diamond stones, getting progressively finer with each stone. This gave a much better finish to the sides, but I had over-filed a few spots that will stay looking not-so-good.
 |
Here's the result: from 1/4" wide to 3/16" wide (flat side shown) |
 |
Side view: logo untouched, but over-filed a bit near the start of the step-down |
This worked out pretty well. I got within a few thousandths of 3/16" at the business end and I'm a few more thousandths over as I go further from the cutting edge. I can live with that.
Next time I'll write about the re-handling.
What diamond stones and grits did you use for this? I find my diamond stones aren't suited for coarse metal removal/shaping but are ok for polishing.
ReplyDeleteRalph, for flattening the backs I started on the extra coarse stone (it says "120 micron" - I don't know how that relates to grit), then through coarse, fine and extra fine. For working on the sides of the 3/16" chisel, I started with coarse files, then finer files, then worked through the coarse, fine and extra fine diamond stones to smooth out the file marks. It did take a bit of time.
Delete